Roundtable targets modern approach to labor shortage
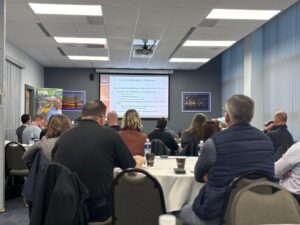
QUINCY — When the subject is automation and workforce in the manufacturing setting, Jeremy Smith makes one thing clear.
“It’s not automation or workforce or workforce or automation. The two really have to go together,” said Smith, a technical specialist with the Illinois Manufacturing Excellence Center.
But a report commissioned by the Upjohn Institute found small- to medium-sized manufacturers lag behind compared to larger manufacturers and often face larger financial, skill set and cultural hurdles in adopting automation technology.
Quincy area businesses and human resources professionals came together Tuesday for the Western Illinois Regional Roundtable focused on modern approaches to address the local labor shortage.
“It’s really just bringing together local organizations and business leaders to get a more in-depth view of workforce resources across the state and locally with a focus on how manufacturers are utilizing automation and showing them ways they also may be able to utilize automation and train their workforce,” said Cole Schwartz, director of workforce and community development with the Great River Economic Development Foundation.
Knapheide Manufacturing Facilities and Maintenance Manager Chuck Makins said the business looks for ways to enhance its workforce — and its automated technology.
“Automation has been a big help to improve our processing out there, shore up some of the labor shortcomings that everyone is having,” Makins said. “We’re always looking for ways to hire new people, especially trades.”
Many manufacturers assume that implementing automation is too costly or only beneficial for large companies, but a slate of speakers challenged those assumptions by sharing strategies for adopting automation technologies and training current employees while also highlighting state and local resources.
“We have to do something,” Smith said. “There’s a continued workforce shortage, so we’ve got to upskill the current workforce, hold onto the current workforce and we’ll need to supplement with automation and other advanced technologies.”
IMA offers similar roundtable programs across the state, working with local partners such as GREDF.
While the financial hurdles may be greater for small businesses, overcoming cultural challenges can be easier.
“For smaller manufacturers with a smaller workforce, making that cultural change, while still not easy, can be simpler to get everyone pulling together,” Smith said.
Manufacturers of all sizes also can turn to a range of financial resources to help overcome financial challenges.
“There’s plenty of automation partners that if given a clear problem statement will be able to put together a cost-effective solution,” Smith said. “The idea is automation should be solving a problem. That problem can’t just be lack of automation. What are we trying to do with this piece of advanced tech equipment, what problem are solving, then we can put together that financial piece.”
Workforce and technology challenges in manufacturing are nothing new.
“The manufacturing industry is still alive, despite the fact all the way back in 1963 we were saying there’s a talent shortage,” Smith said.
But GatesAir HR Generalist Dena Pracht hoped to find some advice because workforce recruiting has gotten harder.
“Because of the environment that we’re in, different challenges with types of business and types of skills we’re looking for, some jobs are harder to recruit for,” Pracht said. “I’ve seen the ebbs and flows over several years, how it changed. I’ll try to get some information on how to more effectively recruit in the market we’re in right now.”
Story By: Quincy Herald Whig – Deborah Gertz Husar – 3/4/25